"Pickles". Yes, I am referring to the undisputed favourite accompaniment to Indian food cuisine.
A few weeks back, I was observing my mother making some lip-smacking mango pickles. However, my focus shifted from the recipe to the process. The striking thing of this process was the swiftness in the whole process with minimal physical touch to the raw mangoes.
And the curious child in me had to ask her 'Why"? She was quick to reply "It is a traditional belief during the making of the pickle; direct contact with your bare hands has a greater chance of your body heat and micro-organisms transferred to the ingredients which may shorten its shelf life."
While this belief amused me, I couldn't help but think about the similarity between this incident and the pharma industry about how we maintain a minimum (in fact, zero) physical contact with the product in the pharma industry. And it re-established my belief that the pharma industry is perhaps the most sophisticated kitchen you can find.
A controlled environment is essential for the handling of certain potent products like APIs, radioactive materials or handling viruses and pathogens to reduce the risk of product contamination. We can achieve by restricting human intervention to the manufacturing process.
Glove ports in Isolators and RABS benefit scientific facilities and manufacturing processes perform responsibilities with zero human contact. The port acts as a shield to the operator, allowing them to manipulate the product inside the isolator. It also protects materials from getting damaged due to moisture or oxidation.
Gloves are critical for handling the materials within the barrier systems. However, faulty gloves can cause a breach to the barrier system that can be perilous. This article delves deep into Gloves used for barrier systems like Isolators breaking them down into
Ø Selection of Gloves
Ø Safety Parameters for using a glove.
SELECTION OF GLOVES -

A detailed understanding of the below points is essential for the selection of gloves.
- Glove Material
- Glove Size
- Glove Type
1.Glove Material:
It offers
- outstanding abrasion resistance
- superior resistance to ozone or oxidising chemicals
- naturally soft and offers greater worker comfort
Ethylene Propylene Diene Monomer Rubber (EPDM)
EPDM can withstand strong impacts like abrasion, UV rays, ozone, ageing, weather and is waterproof. Additionally, EPDM is steam resistant, functions in up to 392 degrees F (200 C) without air, and chemical resistant, including to polar fluids, thus making it a popular choice of material for Gloves.
Neoprene
Neoprene gloves provide safety from chemicals, oils, and other hazardous materials. These gloves are used mostly for heavy-duty protection. Neoprene itself resists degradation better than natural or synthetic rubber which means this type of work gloves will last longer.
Other available materials being Butyl, Nitrile, Viton with their respective advantages.
2.Glove Size:
Glove size is determined based on the operator, taking into account his ability to reach the required material during the manipulation process inside the chamber. A few common parameters mentioned below are taken into account while selecting the glove size.
a) Port Size:
The circular open end of the glove is the port size that is measured in diameter (in inches). To illustrate, a glove with a port size of 6" will fit a circular port that has a diameter of 6". It is important to know that the port's size diameter is not the same measurement as the lay-flat length. In simple words, it is when the length of the cuff measured on a flat surface. Port sizes come in standard sizes of 6", 8", 10", and 12". Usually, the glove sizes can fit a larger port size as the polymer material is stretchable. Thus while evaluating glove for oval ports circumference measurements.
b) Glove Thickness:
Apart from the standard thickness that ranges from 15 mil (0.015" / 0.4mm) to 30 mil (0.030" / 0.8mm, there are gloves materials available depending on the thickness required.
c) Glove Length:
While the standard Isolator Glove length is 32", gloves with lengths of 24", 27", 34" and other lengths may be available.
d) Hand Size:
Gloves with hand size seven to 11 are available the common preferred sizes being 8,9 and 10
e) Hand Orientation:
There is a standard preference for ambidextrous gloves as they fit both hands equally and avoid time figuring out which gloves fit which hand.
3. Glove Type:
Gloves are subjected to regular wear & tear especially towards the operational area, i.e. fingers& palm area. Glove type may be selected based on operational wear & tear resistance or frequency of replacement required.
A uniblock or one-piece glove is a singular glove that extends from the shoulder( at the mouth of the glove port) to fingers. So, if this glove gets damaged near fingers, the whole gloves need to be replaced.
A Glove/Sleeve arrangement provides easy to replace only the glove (cuff ring) part making replacements faster & eliminates unnecessary replacement of sleeve part.
SAFETY PARAMETERS FOR USING A GLOVE
In the Pharmaceutical Industry, certain drugs or substances require careful handling as they may react with the outside environment or cause a threat to the operator and environment. Isolators act as a barrier between the operator area & pharmaceutical process area. Additionally, the installed glove ports make it easy to carry out manual work.
Regular use of gloves can cause wear and tear and ignoring continuous checks, or additional safety can expose the operator to hazardous substances.
a) Under Gloving & Over Gloving:
Under Gloving:
Securing the hands with an additional thin layered glove before placing them inside the isolator glove is under gloving.
Over Gloving:
Over gloving is installing a pair of a relatively thin-layered glove on top of the isolator glove (essentially creating double glove protection). This provides results similar to Under Gloving.
Both the methods offers an added layer of safety in the event of micro ruptures on the glove during operation, thus protecting the operator from direct physical contamination. The gloving methods help in hygiene management and overall increasing the service life of a glove.
b) Regular Macroscopic Checks:
The integrity to glove ports is crucial for maintaining a hygienic environment within the Isolators. One must carry out a visual inspection and physical integrity of the gloves routinely to assess any macroscopic damages, wear and tear signs on a glove to avoid any mishaps during the process.
c) Glove Leak Testing:
Monitoring is essential to assess if there are any defects. Thus leaking testing is imperative to Gloves. Glove Leak Tester is an instrument that monitors the integrity of each glove to carry out the process without any leaks.
The Tester follows the ISO Guidelines (ISO 14644-7 Annex E.5) for performing the glove leak test. This ensures that the glove does not have any significant ruptures which would allow any leaks.
Additional Safety Tips for Gloves Protection:
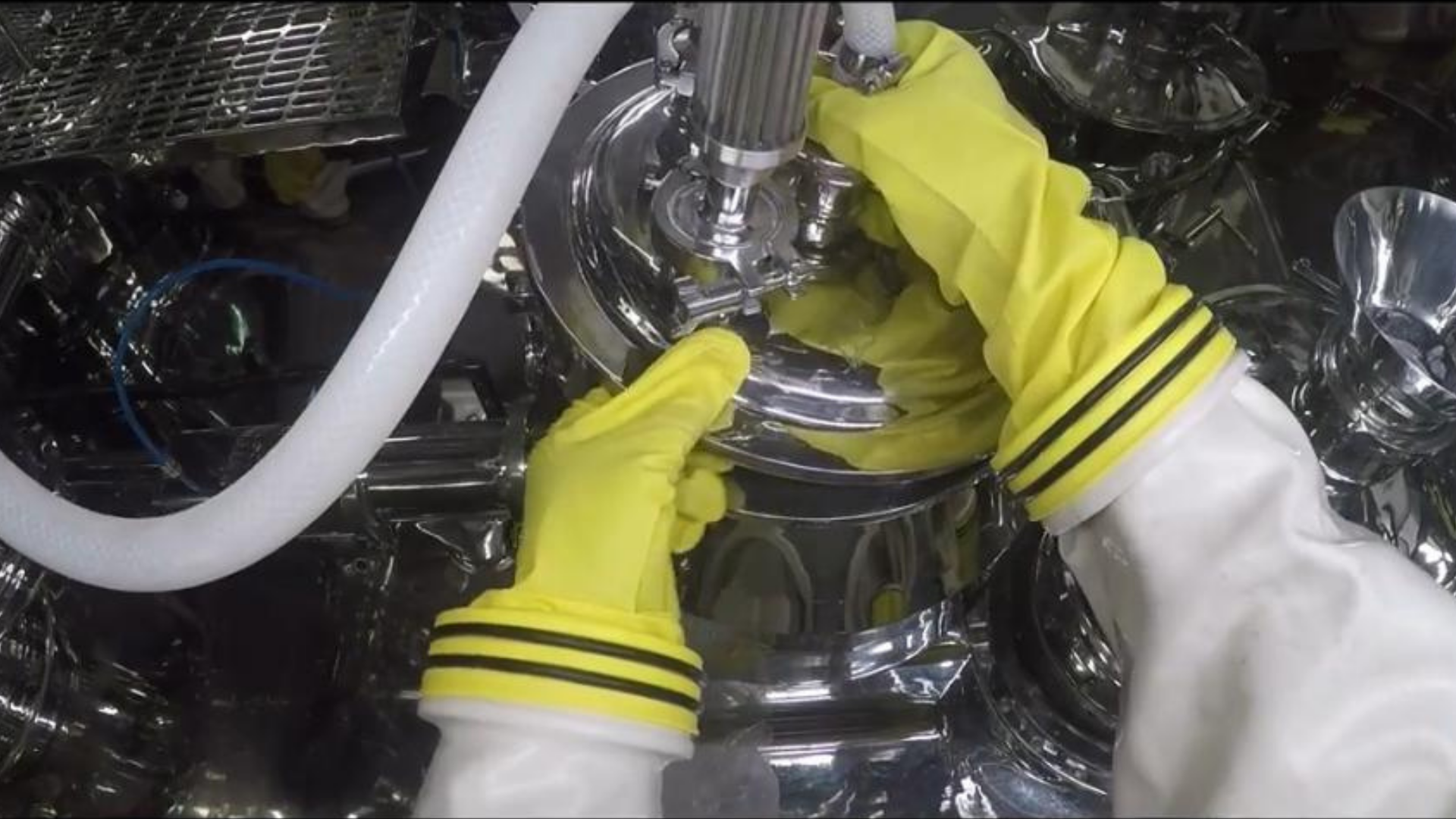
- Hands should be clean & free from any oil or dirt before placing inside a glove.
- Nails should be cut appropriately to avoid any accidental rupture.
- Avoid wearing any finger jewellery which may cause ruptures.
- While handling any sharp objects (scissors in some cases) appropriate care is to be taken.
Conclusion: The Gloves are an excellent tool to minimise human intervention. However, even the tiniest opening in gloves can contaminate the product or be hazardous to the operator. Hence creating SOP Guidelines (Standard Operating Procedures) for Glove testing is crucial.
Please use the form below to know more or to get in touch with us.