As I explained in my previous post, the process through which primary powder particles adhere to form larger multi-particle entities is known as granulation. In this post, I explain various granulation techniques.
Granulation is a step in the preparation of tablets. Granules are prepared agglomerates made up of tinier powder particles. They are generally irregular in shape but can be made into spherical, uniform shapes.
Granulation techniques help to modify and improve the properties of active pharma ingredients which standalone have poor physical properties including low bulk density, poor flowability, poor binding and as such cannot be compressed into tablets.
Granules improve the flow qualities of powders and produce uniform mixtures. They are used to avoid powder segregation, produce dust-free formulations and ensures content uniformity of drugs in individual units. They are also an excellent solution to improve the compaction characteristics of the powder mix. They flow more freely from the hopper or feeding container into die cavities of tablet presses as compared to powders.
Granules also have a smaller surface area compared to a similar powder volume making them more stable both physically and chemically as compared to their powder equivalent. They are less likely to cake or harden. In some instances, they are also far more easily wetted by a solvent as compared to their powder equivalent.
In addition to active ingredients, granules for oral solutions or suspension also contain colourants, flavourings and other ingredients, so the end solution or suspension has all the necessary features of a liquid formulation.
Granules are transformed into effervescent tablets, dispersible tablets, mouth dissolving tablets, melt in mouth tablets, modified release tablets using tablet compression machines.
Compressed tablets must meet quality parameters like uniformity in dosage units, hardness (good strength), friability (no chipping, crumpling or breaking), lower disintegration time and good dissolution rate per determined specifications. The tablet must be stable and retain its efficacy right through to its batch 'best before' date. This is only possible with the right granulation technique and validation of the process.
Granules are prepared by two methods - Dry or wet granulation. Dry granulation includes dry mixing, slug-de-slug and roller compaction processes. Wet granulation includes aqueous granulation and non-aqueous granulation.
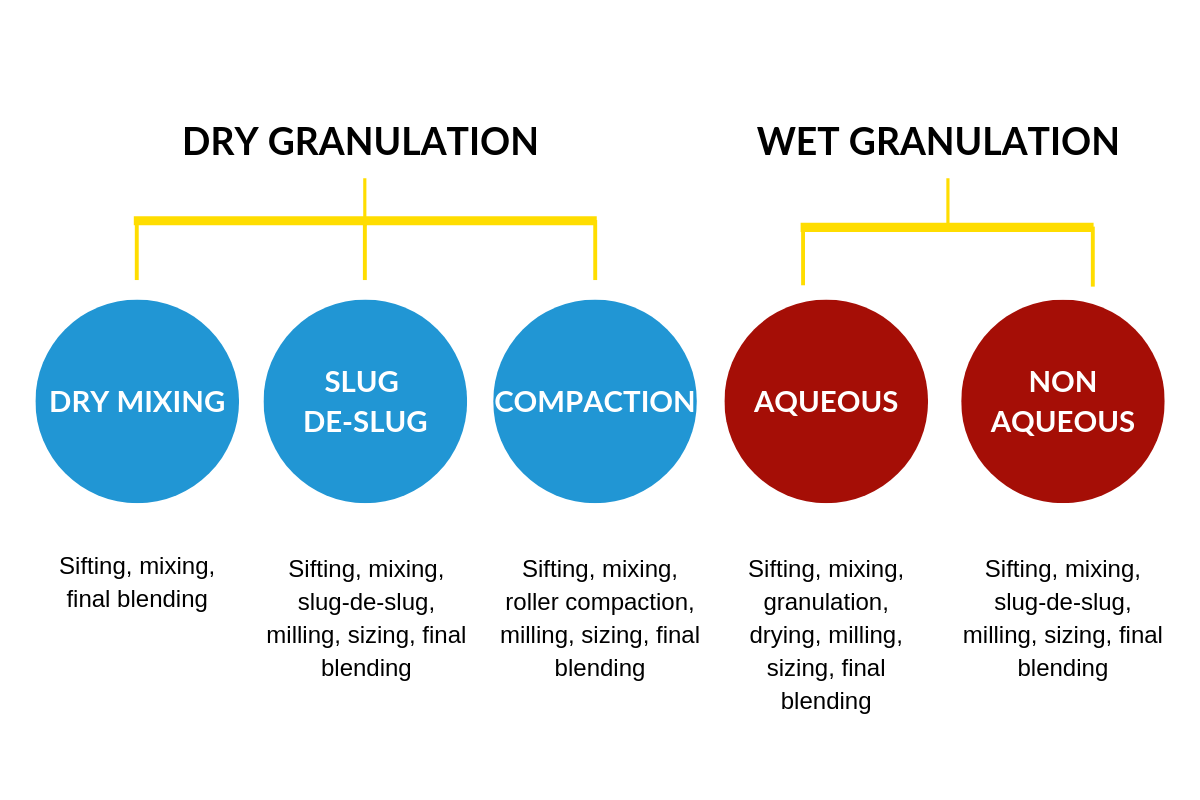
Dry granulation
Dry granulation can be achieved through roller compaction or slugging. Dry powder is passed through a roll compactor which is then granulated to uniform particle size and used to form different textures. Granules created by this method are porous and highly compressible and allow for fast disintegration and modification of release time. This process is excellent for moisture-sensitive drugs. For molecules sensitive to external factors like temperature, moisture can be generated by the dry mixing process. Manufacturers can if needed, select molecules with specified particle size and directly compressible grade of excipients.
Wet granulation
Wet granulation has seen many technical and technological innovations as compared to dry granulation. Molecules that need wet granulation are those not suited for dry granulation process - high dose, poor flow, low in bulk density, without binding properties.
Wet granulation is a widely used technique that produces granules via wet massing of the active pharma ingredient (API) and granulation liquid with or without a binder. Wet granulation is carried out in two ways - one method is to moisten the powder or powder mixture and pass it through a screen of the mesh size needed to produce granules in the desired size using dry heat. The second type used a fluid bed processor in which particles are placed and vigorously dispersed and suspended while liquid excipient is sprayed onto the particles and dried. Depending on molecule sensitivity, aqueous (water) or non-aqueous (organic) solvents are used for the granulation process. Aqueous processes are considered safer and cost-effective.
The most significant disadvantage of wet granulation that it is an expensive process and the loss of material at various stages of processing.
Dry mixing
Dry mixing includes sifting, mixing (drug + bulking agents +binder), final blending (lubricant powders) and compression. Through this process, to achieve good quality tablet, the active ingredient as well as the excipients such as bulking agent, binder, lubricants should support uniform mixing, good bulk density and good flow properties.
Slug-De-Slug
Slug-De-Slug uses tablet compression machines to sift, mix (drug + bulking agents +binder), slug, mill, size, mix (disintegrants), final blend (lubricants) and compress. Slugs are prepared using compression machine, crushed using multi-mill with desired screens, passed through sifters and mixing with lubricants using blenders. The disadvantage of this method is that it has far more processing steps and is a time-consuming process.
Compaction
Compaction is similar to the Slug-De-Slug process and achieved using roller compacters. The powder is fed into the rollers from the hopper which contains a spiral auger to feed the powder into the compaction zone. Compaction takes place between the rollers, producing flakes. Aggregates are screened or milled for production into granules using the appropriate screen size. Granules are then mixed with lubricants using blenders. Compacting is used in the production of directly compressible excipients, drugs and drug formulations, as well as the granulation of inorganic materials, dry herbal materials and immediate/sustained-release formulations. Advantages include lower process times and uniformity in granules particle size distribution as compared to granules produced by the slug-de-slug process.
Aqueous granulation
Aqueous granulation process uses water as a solvent. It includes sifting, mixing and granulation in a Rapid Mixer Grinder with aqueous binder solution, drying in a Fluid Bed Dryer or Processor, milling using a Multi-mill or Co-mill and final mixing in a blender suitable for the task. It is a stable process suited for highly stable molecules, particularly for doses of higher strengths.
Non-aqueous granulation
Non-aqueous granulation process uses organic solvents. As explained earlier in this post, some molecules are sensitive to temperature and moisture, and not suited for dry mixing. These drugs tend to form a high unit percentage of the formulation are manufactured using non-aqueous granulation using organic solvents like Isopropyl alcohol, Dichloromethane, Chloroform as a binder solution. Safety is critical during this process and any equipment used must be flameproof and situated in a dedicated area, and all safety measures adhered to.
Based on the property of the drugs, an aqueous or non-aqueous granulation process can also be developed using a fluid bed processor through a validated recipe, resulting in cycle time reduction.
Advanced granulation techniques have been developed in recent years including Steam granulation, Melt granulation, Foam Granulation.
Steam Granulation
Steam Granulation which is a modification on wet granulation. Steam is used as a binder instead of water. This process has many benefits. It offers higher distribution uniformity, a higher diffusion rate into powders and more favourable thermal balance during drying. Steam granules are more spherical with a large surface area, therefore an increased dissolution rate of the drug from granules. Processing times are shorter, producing more tablets per batch. Steam is far more environmentally friendly as compared to organic solvent. There are no health hazards to the operators, nor are there restrictions by ICH on traces left on the granules. Freshly distilled steam is sterile so the total count can be kept under control. Steam also lowers dissolution rate so it can be used to prepare taste-masked granules without modifying the availability of the drug.
Melt Granulation
Melt Granulation is achieved by the addition of mouldable binder. Mouldable binders are in a solid state at room temperature but melt in the temperature range of 50 – 80˚C. When melted, the binder acts as a binding liquid. This process does not need drying as dried granules are created by cooling down to room temperature.
Foam Granulation
Foam Granulation is when liquid binders are added as aqueous foam. Foam granulation has many benefits over wet granulation as it needs less binder and less water to wet granulate. The foam is added at a greater rate than sprayed liquids leaving no detrimental effects on granulation or tablet. There is no over wetting or plugging problems as spray nozzles are eliminated. This method is handy when granulating water-sensitive formulations. It uniformly distributes binder throughout the powder bed and reduces drying time and therefore manufacturing time. Immediate release and controlled release formulations need much less binder with this process.
This post originally appeared on the Fabtech blog.